Tempering is a heat treatment that is carried out on steel after hardening to achieve…
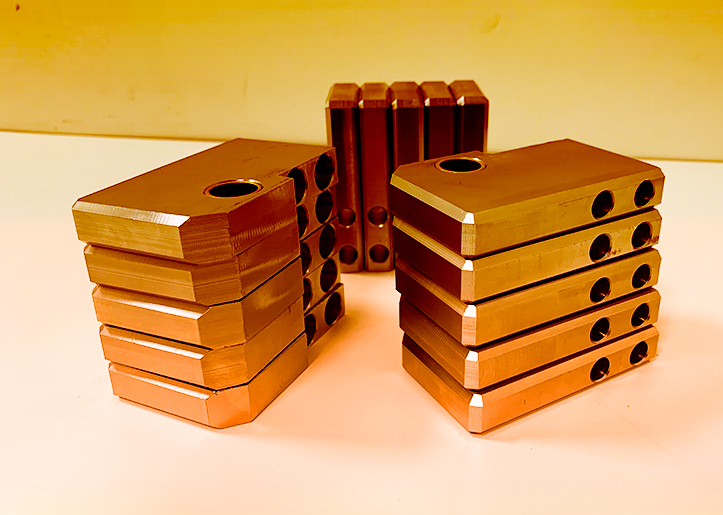
What is the chamfering process and what is it for? | EONSI
Find out what the chamfering technique consists of when manufacturing parts, what the process is like and the main methods that exist.
What is chamfering?
Chamfering is a machining process to remove the edges of parts. Its objectives are to avoid breaking or wear of the edges, to protect people against knocks or friction with a part or simply to avoid burrs in order to favour a more aesthetic finish or to allow the following processes to be carried out.
The chamfering process is a controlled rounding of the edges of the parts. This is done by contouring the silhouettes using special tools.
What is the process of chamfering a material?
Chamfering can be carried out on the outer edges of parts, for example at the ends of a shaft; or on inner edges, as in the case of the leading edges of holes. There are two types of chamfering:
- Corner chamfers. Produced with the corner chamfer tool according to a specific distance, two distances or a distance and an angle.
- Edge chamfers. A type of chamfer that creates a bevelled surface between the two surfaces adjacent to the edge.
Chamfering methods
There are several chamfering methods depending on the tools used, materials to be treated and the technique employed. The most common are:
Mechanical chamfering
Milling machines, shears and chamfering machines are the most common machines used for mechanical chamfering. This process is optimal for mechanised weld preparation, as chamfering workpieces using CNC milling machines facilitates weld seam production.
Milling machines move along the workpiece or work in a hitched position, which makes them very flexible, space-saving and cost-effective to use. Mechanical chamfering, on the other hand, is carried out with shears, so that a long chip is cut from the edge of the sheet metal. An efficient method without dust and noise, ideal for steel parts.
Laser cutting
Chamfering by laser cutting is suitable for a wide range of materials with achievable tolerances of up to +/- 0.1 mm / m. This process allows high cutting speeds, with no burrs and high efficiency. However, they often involve high investment costs and the thickness of the material may limit their use in some cases.
Waterjet cutting
Waterjet cutting is a highly effective method and the ideal alternative to other traditional cutting procedures. The approach is simple: a high-pressure water jet of up to 6,200 bar is directed at the edge, causing controlled rounding of the edges. This chamfering technique is highly effective due to its high precision and lack of thermal stress, although the high costs and slowness of the process must be considered.
Plasma cutting
Despite their high cost, high noise levels and the hardening of the marginal areas due to the fact that it is a chamfering method that is still under development, plasma cutting allows working with high alloy steels and cutting thicknesses of up to 200 mm. In addition, they are characterised by high cutting speeds that allow high production rates.
The choice of chamfering method depends on many criteria. For example, laser cutting is usually the best choice for thin sheets, while waterjet cutting is often used for steel with thicknesses of more than 300 mm. In turn, if the aim is to make the process cheaper, mechanical chamfering is usually chosen.
Common uses of the chamfering technique in parts production
The chamfering technique is used in manufacturing processes for different purposes:
- To facilitate the entry of shafts or screws into holes, making assembly easier.
- Facilitate welds by preparing the joints to increase the penetration of the weld bead.
- Eliminate existing burrs from other machining processes.
EONSI, specialists in the chamfering of parts
EONSI are experts in chamfering, bevelling and cutting parts. We have extensive experience in machining projects based on techniques that include the production of chamfers. Contact us without obligation and we will advise you on the method that best suits your needs.