Know the different types of stainless steel that exist, their main qualities and advantages when…
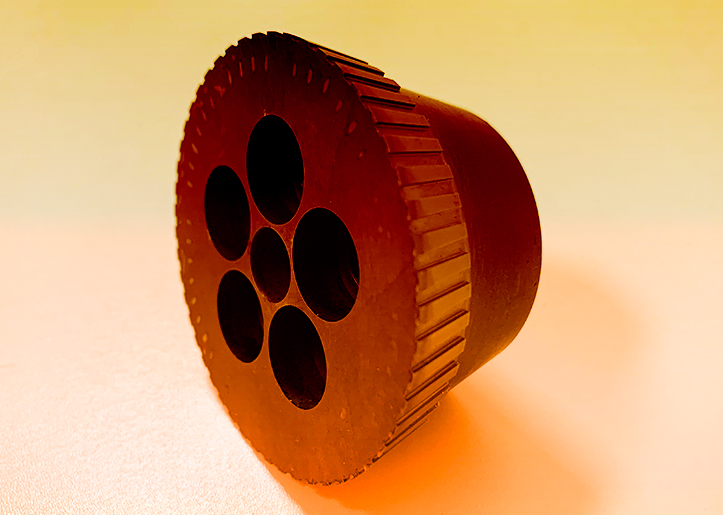
Steel tempering: types, benefits and process | EONSI
Tempering is a heat treatment that is carried out on steel after hardening to achieve the desired toughness and strength. Let us explain it in more detail.
Steel tempering: types, benefits and process
Steel tempering is a thermal process which, like hardening or normalising, is carried out on the metal to achieve the desired hardness and strength, and can be applied to metal parts or masses that have been formed in machining processes. Tempering is carried out after processes such as neutral hardening, double hardening, induction hardening, carburising in atmosphere or carbonitriding. There are several types of tempering depending on the time and temperature with which it is worked, and which are applied depending on the purpose of the workpiece, low temperature tempering, tempering of spring steels, high temperature tempering, and it can also be external or internal.
What is tempering?
Steel tempering involves applying a certain temperature to the metal for a certain period of time to improve its mechanical characteristics, as well as to reduce the internal stresses of the part after hardening or cold deformation, also increasing its ductility and toughness. It is always carried out after the tempering process, which makes the steel brittle, providing hardness and mechanical resistance. The combined application of these two heat treatments is called quenching and tempering.
Types of tempering
There are different types of tempering, depending on temperature and duration. These factors are applied according to what the part is to be used for, the mechanical properties to be obtained, the type of tool, the geometric shape and also the steel chosen. According to this, we can generally differentiate between 3 types of tempering.
Low-temperature tempering
Low temperature tempering uses temperatures between 160 and 300 ºC, with a hardness requirement of around 60 HRC. The process lasts longer than at higher temperatures in order to achieve a homogeneous temperature throughout the part. This process reduces the internal stresses in the steel. It is used for cutting tools that must maintain hardness and wear resistance, case hardening components and for cold work tool steels
High-temperature tempering
High temperature tempering is when we use temperatures higher than 500 °C. This is used for carbon construction steels, hot work tool steels and high speed steels. Tempering at high temperature results in an increase in toughness, the hardness will vary between 300HB and 65HRC depending on the material.
Tempering of spring steels
Tempering at temperatures between 300 and 500°C is applied to spring , coil or die steels. At this temperature, steels with a high yield strength and a firmness suitable to withstand strong bending and torsional stresses are achieved. Generally, the hardness requirement is around 45 HRC.
Tempering systems
Many tempering systems are integrated into fully automated production lines, however, there are certain cases where the process is carried out in separate furnaces. These furnaces, designed specifically for each case, use different heating systems such as oil bath tempering furnaces, salt bath tempering, and forced air recirculation furnace tempering.
Oil bath tempering
There are certain types of oil that can be used for tempering steel. The temperature of the oil is controlled by heaters and circulating pumps and heat exchangers to raise or lower the temperature. The drawback to oil bath tempering is having to remove adhering residues.
Salt bath furnace tempering
Salt bath tempering can be used at different temperatures. It is suitable for all steels as the heating is very homogeneous as it is carried out in several stages, the parts are heated quickly and uniformly as they are immersed in the molten salts.
Forced air recirculation furnace tempering
This type of tempering furnace is the most versatile, with many variants adapted to the needs of the process, the temperature required or the shape of the parts. The forced recirculation of air surrounds the parts in their entirety, guaranteeing rapid and uniform heating. To heat the air, one or more groups of centrifugal motor fans are used to recirculate the air in the most suitable way, and they are also equipped with automatic temperature regulation.
Benefits of tempering steel
The main benefits of steel tempering are as follows:
- It reduces the brittleness of the steel after tempering treatment.
- It gives the desired hardness to the metal.
- It provides high wear and tensile strength.
- It increases the toughness of hardened steels.
- It reduces the internal stresses created during hardening.
- It improves the ductility of machined parts.
Phases of the tempering process
Tempering is applied to hardened steels as they tend to become excessively hard and brittle. There are three stages in the tempering process.
- Heating to a temperature below the critical temperature.
The heating temperature for carbon steels for construction purposes is between 450 and 600°C. The tempering temperature for tool steels is 200 to 350°C. In this phase, the martensite, which is reached by quenching, expels the excess carbon.
- Temperature maintenance.
Tempering at low temperatures lasts longer than at higher temperatures in order to allow time for the temperature throughout the workpiece to be homogeneous.
- Cooling.
The speed of cooling has no influence on the treated material as long as the temperatures do not exceed those that determine the brittle zone of the material. Parts can be cooled in water, but if tempering is carried out at temperatures above the brittle zone, it is advisable to cool them in a hot oil bath at about 150°C and then in water, or in the open air.
Tempering of tools and their temperature
Tool steels are a basic material for the manufacture of all material groups and tool manufacture. A correctly carried out quenching and tempering process is decisive for achieving improvements in the mechanical and functional properties of tools. After quenching, the steel must be cooled and then quickly tempered by heating the workpiece, which must be clean and polished. In addition to the quality and condition of the material, an irregularity in the thermal process can lead to faster wear, deformation, defect of functional elements or even major damage such as cracks in the tools.
The tempering temperature of tools depends on the mechanical properties to be achieved, the type of tool, use, geometry and the steel used. Some examples of tool temperatures:
- 175-220ºC
Hard knives with low flexibility and high edge retention.
- 220-230ºC
Stamping dies, tools for engraving or carving steel, knives with some extra flexibility and good edge retention.
- 230-240ºC
Mortising tools, paper-cutting blades, hammer jaws, large knives, cutting tools requiring some flexibility and shock resistance.
- 240-250ºC
Scissors, rock drills, drill bits, large knives, large cutting tools requiring flexibility and shock resistance.
- 250-260ºC
Gouges, blades, punches, chisels, chisels and stone picks.
- 260-270ºC
Agricultural tools, stone-working tools, wood planing knives.
- 270-280ºC
Axes, hoes, hot-cutting choppers.
- 280-290ºC
Metal scissors, planing knives for planing soft wood, needles, chisels, cold cutting shears.
- 290-310ºC
Wood saws, metal saws, screwdrivers, cutters
- 350-500ºC
Springs, coils and strips
Steel tempering at EONSI
EONSI, as CNC machining specialists, provides the solution for strategic sectors that require steels with very specific properties, such as the aeronautical, medical, optical, food and energy industries, among others. We have cutting-edge technology to improve industrial processes, heat treatment operations such as hardening and tempering of steel, cleaning and polishing surface finishes, which are essential to increase our products’ efficiency.